開発提案事例01
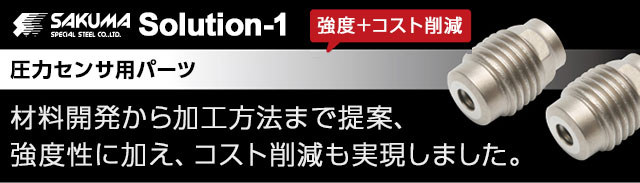
- 担当者:
- チーム長 杉野和博
- 部 署:
- 東海支店 営業第一チーム
- 担 当:
- 加工部品の営業をメインに担当
(部署・役職は開発当時の担当です)
開発背景
対環境性が求められる中で、自動車エンジンも燃費を含め性能の向上がどんどん進んでいます。各種パーツもエンジンスペックに耐えうる品質が求められ、今回、客先より現状流動材料と同等の特性を持ち、且つ高強度の材料提案が求められました。
佐久間の対策・提案
佐久間特殊鋼では、次期型製品への適用であると判断し社内プロジェクトを発足。初回引合いから量産開始まで5年の歳月をかけ、材料特性、部品加工方法について客先、材料メーカー、加工メーカーとの打合せ、試作を重ねました。そして、冷鍛可能な高強度低膨張材の開発と、冷鍛+切削、研磨加工により、高度な要求特性に応えるとともに、コスト削減も付加しながら、量産化を達成しました。
効果
材料開発から部品加工までを当社サプライチェーンと共同で対応することで、QCDにおいて高い優位性を発揮することができました。
開発提案事例02
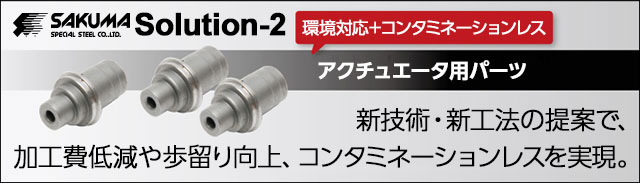
開発背景
客先へのコストダウン提案活動と当社サプライチェーン企業の技術力PRを兼ねて、従来工法から新工法への新しい技術提案を実施。高度な要求仕様に対し、サプライチェーン企業と共同で、最適工法・コストダウン技術の開発プロジェクトをスタートさせました。
佐久間の対策・提案
コストダウンのための新技術・新工法を考える上で、当社がこれまで他のアプリケーションで成功している冷鍛技術を横展開できないか検討を重ね、展開可能と判断。放電穴あけ加工との組合せで新たな技術開発に取組みました。途中、寸法精度面で数々のエラーが発生し、試作トライは2年間で10回以上を数えました。その後もトライ&エラーを重ね、工程改善を加えながら、立ち上げから約3年を経て安定稼動へと繋げることができました。
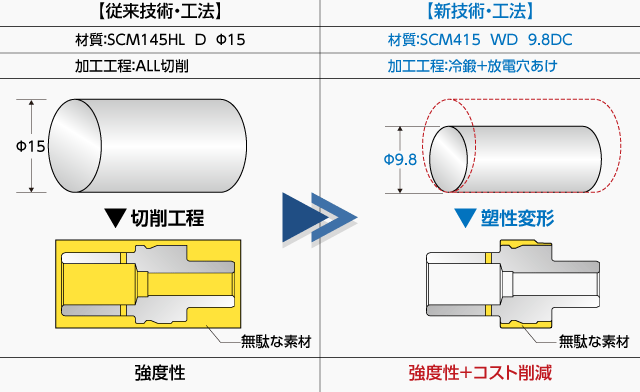
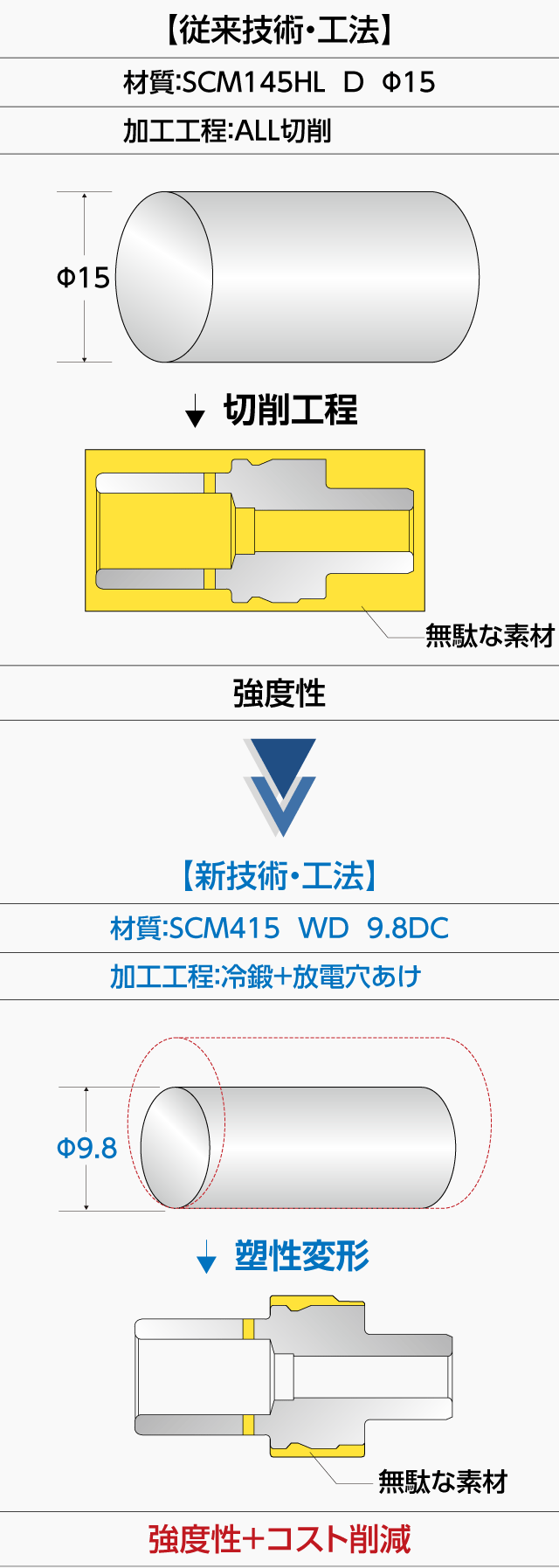
効果
冷鍛化による加工費低減および材料歩留り向上、外径公差20μの保証。放電加工によるコンタミネーションレスの達成。さらにはバリ除去工数の低減などを実現。
この技術提案により、お客様からVA・技術賞を受賞いたしました。